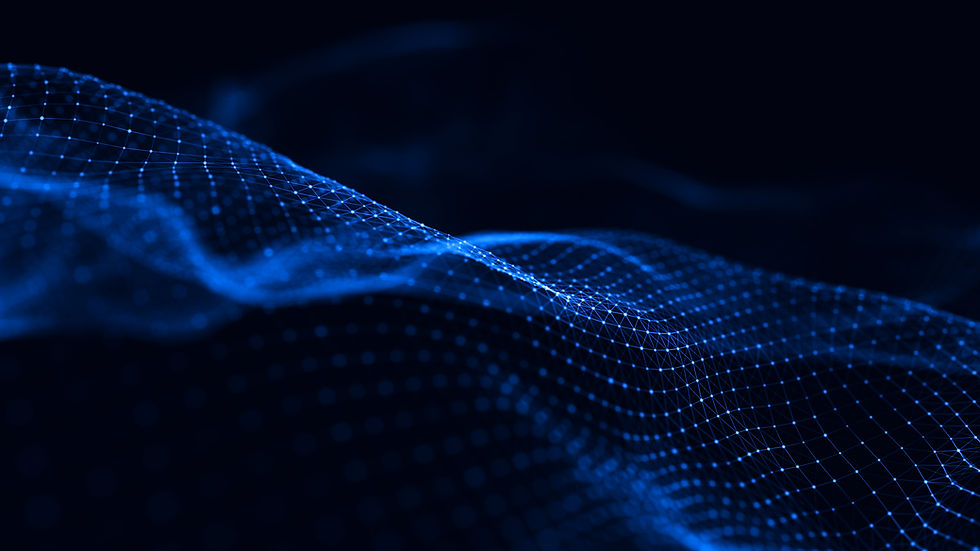
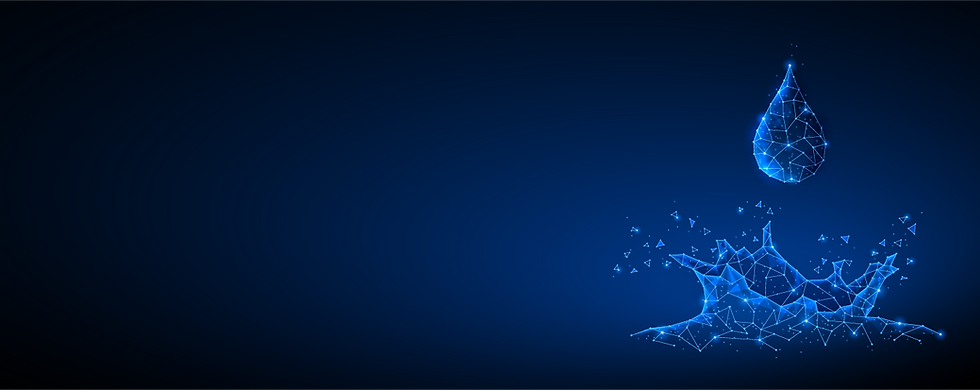
Turbulent Mixing & Separation Technology
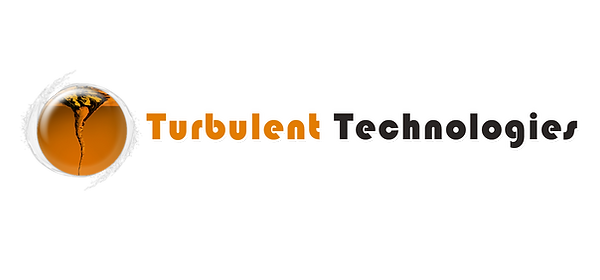
Proprietary technology applicable to a wide range of industrial processes, including Solvent Extraction, Oil and Gas, vegetable oil production and the pharmaceutical industries.
​
We also offer Advanced Custom Mixer Design (rotary and static), and Specialized Consulting Services to solve all your most difficult mixing and separation problems for any application.
Proven Technology
Working at the confluence of hydrodynamics, physics and chemistry, Turbulent Technologies patented “Turbulent Mixing” technology has application to many conventional industries and industrial plants for the mixing and separation of organic and inorganic fluids. Our proven technology quickly demonstrates operational and capital cost savings for customers and is operational at large scale in industrial plants around the world.
​
“Turbulent Mixing” will dramatically improve the mixing and separation of liquid/liquid emulsions, even in the presence of suspended solids, by modifying the drop size distribution in the emulsion. It works with gravity separators, hydrocyclones, flotation, and all separation technologies. Static and rotary implementations are available.


Oil & water don't mix, but they don't separate easily either.
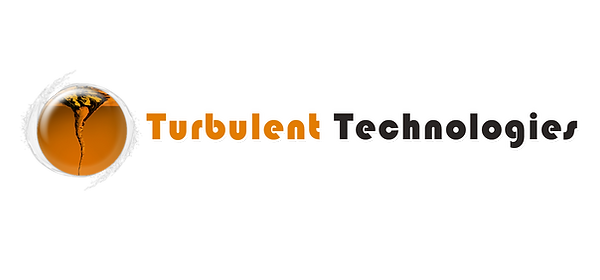
Benefits
Turbulent Mixing technology for applications involving mixing and separation of organic and inorganic fluids (such as Liquid Extraction (SX), Produced Water Treatment, Desalting of Crude, etc) provides:

Improved separation of emulsions

Optimal mass transfer

Increase throughput of existing plant

No additional chemicals

No changes to existing process

Easy retrofit to existing plants

Tolerant of suspended fine solids
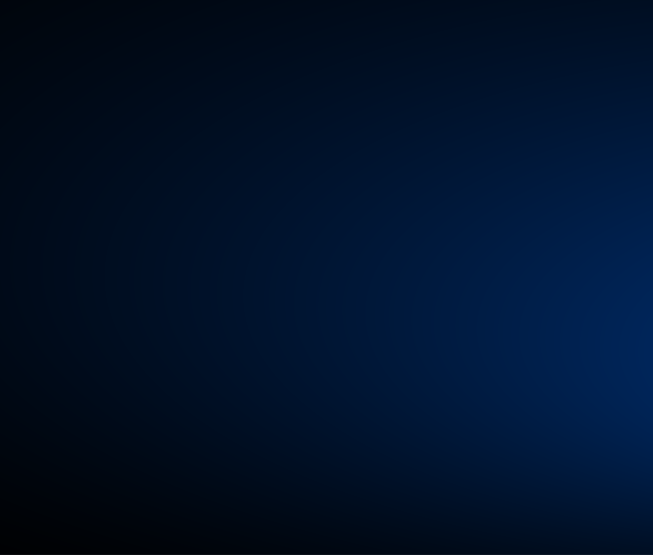
When off the shelf mixers won’t do the job, or if you have process problems related to existing mixers, we can design custom mixing equipment of all types, including chemical reactors, to meet your complex liquid/liquid, liquid / solid and non-standard mixing needs (gas / liquid, different viscosities and densities, and other difficult cases ).
Let us know what your problem is and get a free consultation.